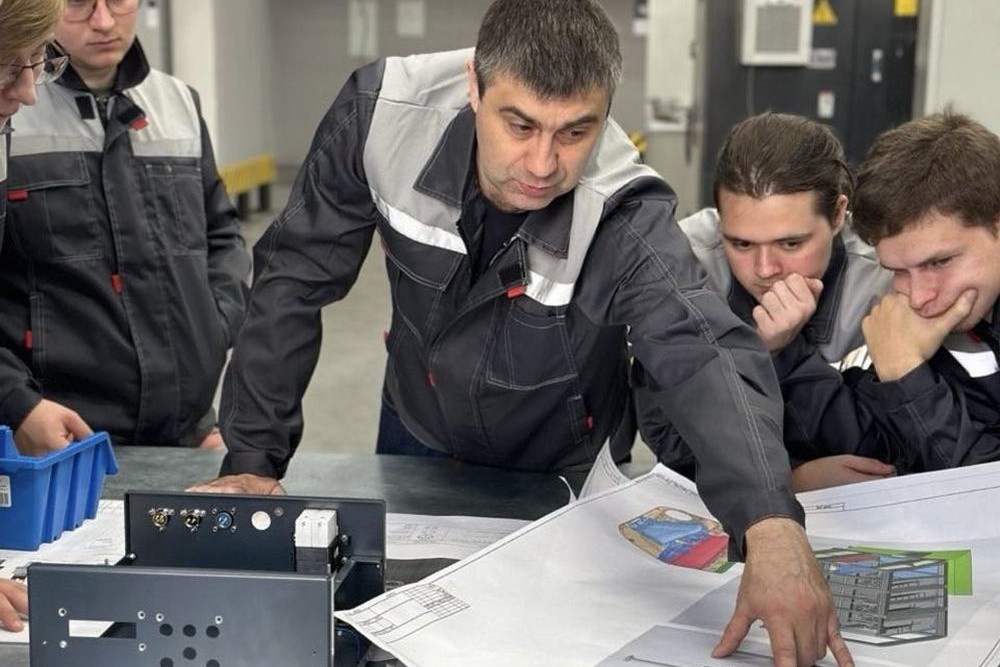
Как пояснил директор ПИШ Александр Селиванов, модернизация включала в себя не только замену импортных модулей ультразвуковой сварки и генераторов на отечественные, разработанные в ТГУ, но и изменение цикла сварки, перепрограммирование контроллеров управления линиями.
– Основная цель – повышение производительности линии и обеспечение ее стабильной работы в массовом производстве при трехсменном режиме работы, – отметил Александр Селиванов. – В общей сложности во всех линиях было установлено 60 ультразвуковых генераторов и 223 ультразвуковые головки для сварки. При этом 80% комплектующих – отечественного производства. Проект был реализован в очень сжатые сроки – в течение восьми месяцев с момента получения университетом номинации, а модернизация всех пяти линий была выполнена в течение трех недель. После модернизации удалось добиться повышения производительности более чем в полтора раза.
Вуз разработал специальные ультразвуковые генераторы с возможностью интеграции с контроллером линии, оптимизирован алгоритм захвата резонансных частот в широком диапазоне, что позволило в автоматическом режиме от одного генератора “запускать” несколько ультразвуковых головок.
Производство ультразвукового оборудования было запущено университетом в первом полугодии 2024 года на базе собственного инновационно-технологического парка, который входит в структуру передовой инженерной школы. С предложением заняться этой разработкой автопроизводитель обратился к вузу, учитывая опыт работы и уровень компетенций специалистов университета в данной сфере: ранее университет сотрудничал с поставщиками автозавода в области технологий ультразвуковой сварки полимерных материалов, а в прошлом году тольяттинский вуз разработал и поставил на автозавод 20 ручных ультразвуковых комплексов.
В реализации проекта участвовали студенты 1-4 курсов обучения – будущие инженеры, которые, занимались производством преобразователей ультразвука, изготовлением вспомогательной технологической оснастки, участвовали в сборке узлов и испытании ультразвуковых колебательных систем, настройки ультразвуковых генераторов. Студенты были привлечены к работе непосредственно на производстве пластмассовых изделий автозавода и участвовали в работах по модернизации – установке в линию ультразвуковых головок, пайки разъемов, прокладке силовой и сигнальной проводки и т.д.
– Сейчас линии уже запущены и работают в три смены. Студенты набирают статистику, фиксируют изменения резонансных частот в цикле работы линий, – рассказывает Александр Селиванов. – Эту аналитику они смогут использовать в своих курсовых работах, отчетах по практикам или в выпускных квалификационных работах. А мы как разработчики воспользуемся этими сведениями для проектирования новых решений в области ультразвукового оборудования. В ПИШ в рамках реализации научной программы мы ставим перед собой цель стать центрами превосходства в области ультразвуковых, магниевых, лазерных технологиях и плазменно-электролитического оксидирования. А для этого нужно уметь не только модернизировать, но и разрабатывать “с нуля” отечественное технологическое оборудование. В рамках сотрудничества с автозаводом мы начинаем проработку проектов по созданию отечественной линейки автоматического и роботизированного оборудования для ультразвуковой сварки. Это не только позволит заводу решить вопросы по импортозамещению, но и обеспечит вклад в технологический суверенитет в рамках нового национального проекта в области станкостроения
Комментарий
Ерохин Павел Иванович, начальник управления технологии автомобиля Дирекции по технологии автомобиля по проектам автопредприятия:
– В результате выполненных работ была увеличена производительность текущего оборудования с 28 до 45 авто в час, а также повышена стабильность работы оборудования с 85% до 95%. В целом, команда проекта удовлетворена выполненными работами на объекте. Есть точки роста в организации и реализации подобных проектов, которые, уверен, будут решены в результате совместного сотрудничества. Проведенная модернизация должна привести к сокращению времени ремонта в связи с уменьшением количества поломок, к увеличению производительности оборудования, к снижению затрат на время работы оборудования и на закупаемые запасные части. В дальнейшем планируем продолжить сотрудничество с университетом по новым крупным проектам.